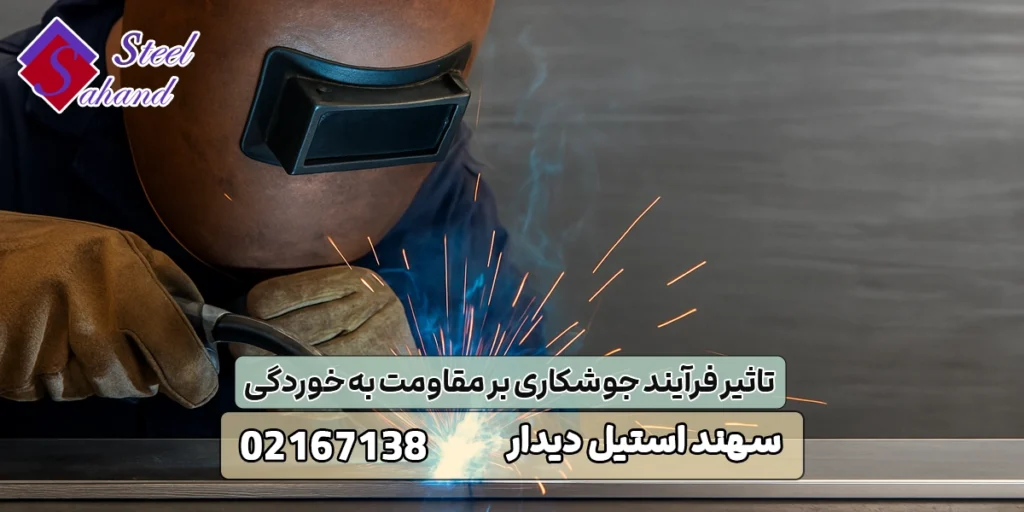
در صنایع مختلف مانند نفت، گاز، پتروشیمی، خودروسازی و ساختوساز، یکی از چالشهای اصلی حفظ طول عمر تجهیزات فلزی در برابر خوردگی است. در این میان، تأثیر فرآیند جوشکاری بر مقاومت به خوردگی بهعنوان یک عامل کلیدی در طراحی و بهرهبرداری از سازههای فلزی مورد توجه قرار میگیرد. فرآیند جوشکاری، اگرچه برای اتصال دائم قطعات فلزی به کار میرود، میتواند ویژگیهای متالورژیکی فلز را تغییر داده و نواحی جوشخورده را نسبت به خوردگی آسیبپذیرتر کند.
ناحیه حرارت دیده و مقاومت به خوردگی
در حین جوشکاری، ناحیهای به نام منطقه تحت تاثیر حرارت (HAZ) به شدت تحت تاثیر دمای بالا قرار میگیرد. این منطقه بدون ذوب شدن تغییر ساختار میدهد و ممکن است دچار دگرگونیهای متالورژیکی شود. تغییر در اندازه دانهها، ایجاد تنشهای پسماند و حذف یا تغییر ترکیب عناصر آلیاژی از جمله عواملی هستند که باعث میشوند مقاومت به خوردگی در این ناحیه کاهش یابد.
انواع فرآیندهای جوشکاری و اثر آنها بر مقاومت به خوردگی
جوشکاری قوسی با الکترود دستی (SMAW)
این روش رایجترین نوع جوشکاری است. بسته به نوع الکترود مصرفی، لایه محافظی روی سطح ایجاد میشود که تا حدودی میتواند در برابر خوردگی از فلز محافظت کند. با این حال، باقیماندههای فلاکس اگر به خوبی پاک نشوند، باعث ایجاد خوردگی موضعی میشوند.
جوشکاری قوسی با گاز محافظ (GMAW/MIG و GTAW/TIG)
در این روشها استفاده از گاز محافظ مانند آرگون، از اکسید شدن حوضچه مذاب جلوگیری میکند. فرآیند جوشکاری بر مقاومت به خوردگی در این تکنیکها معمولاً بهتر کنترل میشود و نواحی جوشخورده از کیفیت سطحی بالاتری برخوردار هستند.
جوشکاری لیزری و الکترونی
این روشهای پیشرفته به دلیل دقت بالا و حرارت ورودی پایین، باعث کاهش تغییرات متالورژیکی میشوند. در نتیجه، خوردگی کمتری در محل جوش اتفاق میافتد.
عوامل موثر بر خوردگی در ناحیه جوش
در فرآیند جوشکاری، ناحیه جوش و اطراف آن به دلیل تغییرات حرارتی و ساختاری، دچار تغییراتی میشوند که به طور مستقیم بر مقاومت به خوردگی تاثیر میگذارند. یکی از مهمترین عوامل، ایجاد ترکهای میکروسکوپی در اثر تنشهای حرارتی است که میتوانند به عنوان نقاط شروع خوردگی عمل کنند. همچنین اختلاف پتانسیل گالوانیکی بین فلز پایه و فلز پرکننده، باعث تسریع در خوردگی گالوانیکی میشود، بهخصوص در محیطهای مرطوب یا خورنده که الکترولیت در دسترس است. این موضوع بهوضوح نشان میدهد که تاثیر فرآیند جوشکاری بر مقاومت به خوردگی به نوع مواد مصرفی و شرایط فرآیند وابسته است.
از سوی دیگر، وجود ناخالصیها و آخالهای فلزی به ویژه در جوشکاریهای دستی، محیط مناسبی برای تجمع رطوبت و آغاز خوردگی موضعی فراهم میکنند. همچنین به دلیل نرخ سرد شدن متفاوت ناحیه جوش نسبت به فلز پایه، ساختار میکروسکوپی در این نواحی همگن نبوده و این عدم همگنی ساختاری باعث افزایش حساسیت به خوردگی میشود. به همین دلیل، توجه به اصول فنی و انتخاب فرآیند جوشکاری مناسب، در ارتقاء مقاومت به خوردگی و افزایش عمر سازههای فلزی نقش اساسی دارد. در واقع، فرآیند جوشکاری بر مقاومت به خوردگی تأثیری تعیینکننده دارد و نباید از آن چشمپوشی کرد.
بررسی تاثیر فرآیند جوشکاری بر مقاومت به خوردگی ورق استیل
فرآیند جوشکاری تأثیر مستقیمی بر خواص سطحی فلزات دارد و یکی از مهمترین جنبههای آن، تأثیر فرآیند جوشکاری بر مقاومت به خوردگی است. در حین جوشکاری، حرارت بالا موجب ایجاد تنشهای پسماند، تغییر ساختار کریستالی و بروز ترکهای میکروسکوپی در ناحیه جوش و اطراف آن میشود؛ این عوامل زمینهساز آغاز خوردگی بهویژه در محیطهای خورنده هستند. این موضوع در مورد ورق استیل که به دلیل مقاومت بالا در برابر زنگزدگی انتخاب میشود، اهمیت دوچندان دارد؛ زیرا جوشکاری نادرست میتواند بخشی از مزیت ضد خوردگی استیل را از بین ببرد و موجب کاهش طول عمر قطعات شود.
از طرف دیگر، اختلاف پتانسیل گالوانیکی بین فلز پایه و فلز پرکننده، در صورت استفاده از متریال ناسازگار، میتواند باعث بروز خوردگی گالوانیکی در ورقهای استیل جوشخورده شود. همچنین، نرخ سرد شدن سریع در محل جوش ممکن است باعث ایجاد ساختارهای ناهمگن شده و مقاومت به خوردگی را کاهش دهد. بنابراین، برای حفظ ویژگیهای ذاتی استیل مانند مقاومت بالا در برابر خوردگی، لازم است فرآیند جوشکاری با دقت بالا و با انتخاب صحیح مواد پرکننده، گاز محافظ و روش مناسب انجام شود. در واقع، فرآیند جوشکاری بر مقاومت به خوردگی ورق استیل اثر تعیینکنندهای دارد و رعایت استانداردهای فنی، تضمینکننده دوام و عملکرد مطلوب در شرایط صنعتی خواهد بود.
راهکارهای بهبود مقاومت به خوردگی پس از جوشکاری
استفاده از مواد پرکننده سازگار: انتخاب صحیح فلز پرکننده مطابق با فلز پایه میتواند از اختلاف پتانسیل گالوانیکی جلوگیری کند.
انجام عملیات حرارتی پس از جوشکاری (PWHT): این کار تنشهای پسماند را کاهش داده و ساختار فلز را یکنواخت میکند.
پاکسازی دقیق محل جوش: به ویژه در روشهای SMAW یا FCAW برای حذف باقیمانده فلاکس.
پوششدهی ضد خوردگی: مانند استفاده از رنگهای اپوکسی، گالوانیزه کردن یا روکشهای مقاوم به خوردگی.
نتیجه گیری
با توجه به آنچه بیان شد، تاثیر فرآیند جوشکاری بر مقاومت به خوردگی یکی از موضوعات حیاتی در طراحی صنعتی و نگهداری تجهیزات فلزی است. نوع فرآیند جوشکاری، دمای واردشده، نوع فلز پرکننده و عملیاتهای پس از جوشکاری، همگی بر کیفیت نهایی جوش و مقاومت آن در برابر عوامل خورنده تاثیر دارند. با انتخاب صحیح روش جوشکاری و رعایت اصول فنی، میتوان بهطور چشمگیری از بروز خوردگی جلوگیری کرد و طول عمر تجهیزات را افزایش داد.
سوالات متداول
خیر. فرآیندهایی مانند TIG یا لیزری به دلیل حرارت کمتر و دقت بالا، تأثیر منفی کمتری دارند.
بله. با عملیات حرارتی پس از جوشکاری و استفاده از پوششهای محافظ، میتوان تا حد زیادی مقاومت را افزایش داد.
وجود تنش پسماند، ناخالصیها و تغییر ساختار کریستالی از جمله دلایل این مسئله هستند.